Automatic Liquid Syrup Manufacturing Plant
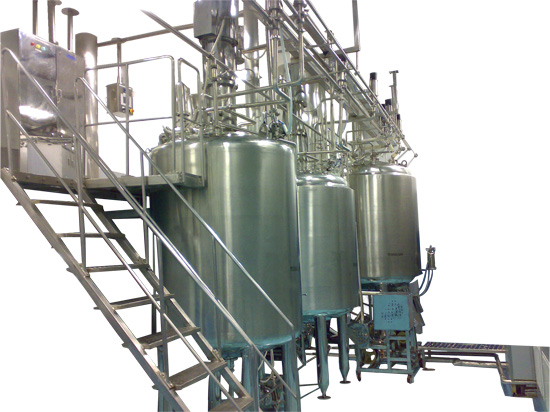 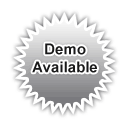
The Liquid Manufacturing Plants are ideal tools for the pharmaceutical industry for the production of Oral Liquids. It is specially designed to take care of two critical factors which directly affect the quality of the Liquids. Minimum manual handling of Liquid.
Effective cleanness during manufacturing. Capacity ranges from 50 L to 20,000 L.
Needless to say, it also provides the benefits of the effective manpower utilization.
Liquid Manufacturing Plant consists :
- Sugar Melting Vessel
- Pre-filtration unit
- Syrup Manufacturing Vessel
- Filtration unit
- Storage Vessel
- Control Panel
- Product Piping
- Working Platform
- This system consists of a closed circuit manufacturing facility from feeding of Sugar / Water Phase to loading the Liquid
Filling Machine.
- The Sugar and Water, are load with vacuum system or by mechanical system or manually.
- The Sugar Syrup Vessel is supplied with high speed stirrer & electrical heating (In small model) / steam heating facility
(In bigger size model) .The sugar syrup is prepared at required temperature & are transferred to Manufacturing Vessel
by vacuum or by transfer pump.
- The product during emulsion formation is recalculated through In-Line Homogenizer or Liquid Transfer Pump.( Optional
Facility )
- The Pump also discharges the product in the Storage Vessel.
- The Storage Vessel is then taken to the filling area (if it is small capacity) and is connected to again Liquid Transfer
Pump. Or Storage Vessel remains fixed (In bigger size) & pump transfer the Liquids in the float tank which is connected
with filling machine.
- The entire Plant can be operated by centralized operating panel by one operator.
Salient Features:
- The Plant is designed to be operated only by one operator and one helper.
- All material transfers are done by vacuum or by transfer pumps.
- All the vessels are CGMP (paint free construction)
- The gaskets used are of silicon (food grade).
- All contact parts are of S.S. 304 quality material (SS316 provided on demand) & finished to class 4B (Mirror) finish and
are crevice free.
- The entry of stirrer & high speed emulsifier are from top. In-line Emulsifier (as per customer choice) provided on
demand.
- All vessels are suitable for internal pressure of 1 Kg. / Sq. cm. and hence can be sterilized.
- All pipes, pipe fittings and valves are of SS304 / SS316 (as per customer requirement) seamless quality, internally
electro polished, with tri-clover ended joints.
Filter Press
Operation :
The unfiltered liquid is fed into the filter under positive pressure, where liquid travels in downwards direction and finds its way through opening on sides of the Filter Plates.
As the liquid pressure increases, the Filter media holds the foreign particles and allows only clear filtrate to pass through the central channel formed by interlocking pressure cups to the outlet. Filtration is continued until the cake holding capacity of the unit is reached or until the filtrate rate becomes too slow owing to cake resistance.
Technical Specification :
Types |
Diameter of Plate |
No. of Plates |
Filtering Area M2 |
Cake Capacity |
Output Ltr / Hr |
S86 |
8" |
6 |
0.1886 m2 |
4.34 liters |
400 |
S88 |
8" |
8 |
0.2260 m2 |
5.79 liters |
500 |
S148 |
14" |
8 |
0.6130 m2 |
27.78 liters |
1000 |
S1410 |
14" |
10 |
0.7960 m2 |
34.72 liters |
1200 |
S1812 |
18" |
12 |
1.745 m2 |
78.01 liters |
4000 |
S1815 |
18" |
15 |
2.169 m2 |
40.50 liters |
5000 |
S1823 |
18" |
23 |
3.338 m2 |
63.49 liters |
7000 |
S2410 |
24" |
10 |
2.53 m2 |
142.56 LITERS |
9000 |
S2418 |
24" |
18 |
4.37 m2 |
113.12 LITERS |
16,200 |
S2413 |
24" |
13 |
3.22 m2 |
185.33 LITERS |
11,700 |
S2424 |
24" |
24 |
5.75m2 |
150.81 LITERS |
21,000 |
|